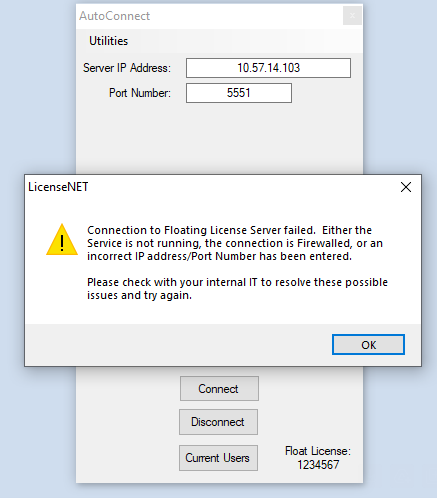
7. User cannot Connect to the Float License Server
User getting “Connection to Floating License server has failed The user may also get a
It’s old news that people are rethinking their priorities and making career moves during the pandemic, but increasingly, more workers are already considering moves when the pandemic ends. According to a special report in the “Pulse of the American Worker,” from Prudential Insurance in March 2021, 20% of workers “changed their line of work entirely over the past year.” Half of those said the move was permanent. Of concern to many employers, however, is that an additional 26% of workers are saying that they plan to look for work with a different employer when the pandemic eases.
These massive changes and the influx of new hires make it difficult for all employers, however, it’s even more treacherous for manufacturing and production entities who have safety issues that go beyond PPE and hygiene. In 2020, 2.7 million U.S. workers were injured on the job (1), costing businesses over a billion dollars a week. More tragically, 5333 were killed in job-related injuries (2). And 2020 was before the “Big Quit.”
It’s difficult enough to keep your seasoned employees from taking shortcuts, but it’s a whole new ballgame to ensure that the new recruits are trained, and by that we mean, proper training rather than hand-me-down training from someone who does cut corners.
Employers need to ensure full engagement. Management, supervision and employees must work together and collaborate to develop a safety strategy that is embraced by everyone in the organization. And it begins with every stakeholder’s understanding of what the consequences of an accident might be. It’s the only way that a company can build, grow, and sustain a safety mentality and culture. Safety must be a focus on scorecards, appraisals, onboarding training, recurrent training, and an integral part of behavior.
Achieving a true safety culture pays dividends. Apart from the significant financial benefits of an effective safety culture, employees will feel that the company cares, and that engenders loyalty, a valuable asset to retain your workforce. A note of caution, however; If your safety strategy has the depth of a safety poster here and there, you’ll actually be adding to the reasons why people will leave.
“Double-dipping” video work instruction. One simple and cost-effective way to boost your safety efforts is through the creation of video work instructions that can double as safety videos. Video work instructions are the best way to train workers in the right way to carry out a task, and with a lot of new workers, it’s your best chance to make that happen. Video work instruction software such as Timer Pro has storyboard options to facilitate powerful presentations.
A final tip. Having effective and safety-conscious work instructions will ensure that your supervisors are involved with the process. Don’t forget that the supervisors are supervising both production and safety at the same time, so it might also be a good idea to create video work instructions with suggestions showing the right way to supervise a safety intervention. Help your supervisors supervise. They were one of the workers not long ago and managing their former co-worker may be difficult, and if it’s too difficult, you could have an industrial injury to cope with.
User getting “Connection to Floating License server has failed The user may also get a
The DIW Rolex Cosmograph Daytona Ref. 116500LN takes the iconic Daytona model to the next
This error message is usually caused by a random corruption in one of the support
This error message can occur when working with Excel workbooks that have been created or
Unable to Cast COM Object of Type – Can’t Load Library This error message may
This error message may be because Excel is not configured properly. Either a previous or